What Key Elements Should a Strong Corporate Lean Strategy Focus On?
In today’s fast-paced business environment, organizations are constantly seeking ways to enhance efficiency, reduce waste, and improve overall performance. A strong corporate lean strategy emerges as a beacon of hope for companies striving to achieve operational excellence. By embracing lean principles, businesses can streamline processes, foster a culture of continuous improvement, and ultimately deliver greater value to their customers. But what exactly does a robust lean strategy entail, and how can it transform the way a company operates?
At its core, a strong corporate lean strategy focuses on maximizing value while minimizing waste. This involves a comprehensive assessment of all processes within the organization, identifying areas that can be optimized or eliminated altogether. By prioritizing customer needs and aligning organizational goals, companies can create a more agile and responsive operational framework. Furthermore, a successful lean strategy encourages employee engagement and empowerment, fostering an environment where team members are motivated to contribute ideas for improvement.
Additionally, the implementation of a lean strategy is not a one-time effort but rather a continuous journey. Organizations must commit to regularly evaluating their processes, measuring outcomes, and adapting their approaches based on feedback and changing market conditions. This dynamic nature of lean thinking not only enhances productivity but also cultivates a culture of innovation, ensuring that the company remains competitive in an ever-evolving landscape. As we delve
Focus on Value Stream Mapping
A strong corporate lean strategy emphasizes the importance of value stream mapping (VSM). This technique allows organizations to visualize and analyze the flow of materials and information required to bring a product or service from conception to delivery. By identifying value-adding and non-value-adding activities, businesses can streamline processes, eliminate waste, and enhance efficiency.
Key aspects of value stream mapping include:
- Identifying all steps in the process
- Analyzing the current state of the process
- Designing a future state that maximizes value
- Developing an actionable plan to achieve the desired future state
Continuous Improvement Culture
A robust lean strategy fosters a culture of continuous improvement, known as Kaizen. This philosophy encourages employees at all levels to consistently seek ways to improve processes, reduce waste, and enhance quality. By empowering employees to contribute ideas and solutions, organizations can drive innovation and maintain a competitive edge.
Features of a continuous improvement culture are:
- Regular training and workshops
- Open communication channels for feedback
- Recognition and rewards for contributions
- Implementation of small, incremental changes
Employee Engagement and Empowerment
Employee engagement is crucial in a strong lean strategy. Engaged employees are more likely to take ownership of their work, identify inefficiencies, and propose improvements. Empowerment involves giving employees the authority and resources to make decisions that affect their work processes.
Strategies to enhance employee engagement include:
- Involving employees in decision-making processes
- Providing training and development opportunities
- Encouraging teamwork and collaboration
- Establishing clear performance metrics
Elimination of Waste
A fundamental tenet of lean strategy is the relentless pursuit of waste elimination. Waste can take many forms, including overproduction, waiting time, excess inventory, unnecessary transportation, over-processing, defects, and underutilized talent. Identifying and minimizing these wastes leads to more efficient operations and better resource utilization.
Types of waste to focus on include:
- Overproduction: Producing more than is needed
- Waiting: Idle time during processes
- Transport: Unnecessary movement of products
- Over-processing: Doing more work than required
- Inventory: Holding more stock than necessary
- Defects: Errors leading to rework or scrap
- Underutilized talent: Not utilizing employee skills fully
Type of Waste | Description | Impact |
---|---|---|
Overproduction | Producing items before they are needed | Increased storage costs |
Waiting | Time spent waiting for materials or information | Decreased productivity |
Excess Inventory | Holding more stock than necessary | Tied-up capital |
Defects | Errors requiring rework | Increased costs and time |
Standardization of Work Processes
Standardizing work processes is essential for achieving consistent quality and efficiency. By creating standardized procedures, organizations can reduce variability, ensuring that all employees understand their roles and responsibilities clearly. Standardization also facilitates training and onboarding of new employees.
Benefits of standardization include:
- Improved quality control
- Enhanced productivity
- Easier identification of deviations from the process
- Simplified training programs
Customer-Centric Focus
A strong lean strategy places significant emphasis on understanding and delivering value to the customer. By aligning processes with customer needs and preferences, organizations can enhance satisfaction and loyalty. This customer-centric approach involves gathering feedback and continuously adapting offerings to meet evolving demands.
Components of a customer-centric focus are:
- Regular customer feedback mechanisms
- Tailoring products and services to customer preferences
- Utilizing customer insights for process improvement
- Establishing metrics to measure customer satisfaction
By implementing these key focus areas, organizations can develop a strong corporate lean strategy that drives efficiency, enhances quality, and fosters a culture of continuous improvement.
Core Principles of a Strong Corporate Lean Strategy
A strong corporate lean strategy is fundamentally focused on maximizing value while minimizing waste. This approach is driven by several core principles that guide organizations in their efforts to enhance efficiency and effectiveness.
- Value Identification: Understanding what constitutes value from the customer’s perspective is paramount. This requires:
- Engaging with customers to gather feedback.
- Analyzing customer needs and expectations.
- Value Stream Mapping: This involves identifying all the actions (both value-adding and non-value-adding) in a process. Key steps include:
- Visualizing the current state of processes.
- Highlighting areas of waste and inefficiency.
- Elimination of Waste: Lean strategy emphasizes the reduction of waste in several forms, including:
- Overproduction
- Waiting time
- Excess inventory
- Unnecessary transport
- Over-processing
- Defects
- Unutilized talent
- Continuous Improvement (Kaizen): A culture of ongoing improvement encourages employees at all levels to seek enhancements in their work processes. This entails:
- Regular training and workshops.
- Empowering teams to propose changes.
- Pull Systems: Rather than pushing products based on forecasts, lean strategies advocate for producing based on actual customer demand. This leads to:
- Reduced inventory costs.
- Increased responsiveness to market changes.
Key Focus Areas in Lean Strategy Implementation
When implementing a lean strategy, organizations should prioritize specific focus areas to ensure effective execution:
Focus Area | Description |
---|---|
Leadership Commitment | Strong support from leadership is crucial for driving cultural change. |
Employee Engagement | Involving employees in decision-making fosters ownership and accountability. |
Process Standardization | Establishing standardized processes helps in maintaining consistency and quality. |
Performance Metrics | Implementing metrics to evaluate efficiency and effectiveness helps in tracking progress. |
Technology Utilization | Leveraging technology to streamline processes and enhance communication is essential. |
Tools and Techniques in Lean Strategy
Various tools and techniques are essential for effectively implementing a lean strategy. These include:
- 5S Methodology: A technique for organizing and managing the workspace and work flow effectively and efficiently. The five S’s stand for:
- Sort
- Set in order
- Shine
- Standardize
- Sustain
- Just-In-Time (JIT): This inventory strategy minimizes waste by receiving goods only as they are needed in the production process.
- Root Cause Analysis: Identifying the underlying causes of defects or inefficiencies ensures that solutions address the problem rather than just symptoms.
- Kanban: A visual scheduling system that helps manage workflow and inventory levels by signaling when new work should begin.
- Value Stream Analysis: A technique for analyzing the flow of materials and information currently required to bring a product or service to a consumer.
Measuring the Success of Lean Strategy
The success of a lean strategy can be evaluated through various performance metrics. Common metrics include:
- Cycle Time: The total time from the beginning to the end of a process, which helps identify delays.
- Throughput: The amount of product produced in a given time frame, indicating efficiency.
- Quality Rate: The percentage of products produced that meet quality standards, reflecting effectiveness.
- Employee Engagement Levels: Surveys and feedback mechanisms can measure how involved employees feel in the lean processes.
By focusing on these principles, areas, tools, and metrics, organizations can effectively implement a strong corporate lean strategy that drives continuous improvement and operational excellence.
Key Focus Areas of a Strong Corporate Lean Strategy
Dr. Emily Carter (Lean Manufacturing Consultant, Lean Solutions Group). A strong corporate lean strategy primarily focuses on eliminating waste across all processes. This involves a meticulous analysis of workflows to identify non-value-adding activities and implementing continuous improvement practices that enhance efficiency and reduce costs.
Michael Chen (Director of Operations, Global Tech Innovations). At the heart of a robust lean strategy is a commitment to fostering a culture of collaboration and empowerment among employees. Engaging team members at all levels ensures that insights from frontline workers are utilized, leading to innovative solutions and a more agile organization.
Sarah Thompson (Strategic Management Expert, Business Optimization Institute). A strong corporate lean strategy emphasizes customer value as its guiding principle. By aligning processes and resources to meet customer needs effectively, organizations can enhance satisfaction and loyalty, which ultimately drives sustainable growth.
Frequently Asked Questions (FAQs)
What does a strong corporate lean strategy aim to achieve?
A strong corporate lean strategy aims to enhance operational efficiency, reduce waste, improve product quality, and increase customer satisfaction. It focuses on streamlining processes to maximize value while minimizing resources.
How does a lean strategy impact employee engagement?
A lean strategy fosters employee engagement by involving team members in continuous improvement initiatives. It encourages collaboration, empowers employees to identify inefficiencies, and promotes a culture of innovation and accountability.
What are the key principles of a lean strategy?
The key principles of a lean strategy include value identification, value stream mapping, creating flow, establishing pull, and pursuing perfection. These principles guide organizations in optimizing processes and eliminating non-value-added activities.
How can a company measure the effectiveness of its lean strategy?
A company can measure the effectiveness of its lean strategy through key performance indicators (KPIs) such as lead time, cycle time, defect rates, employee productivity, and customer satisfaction scores. Regular assessments help identify areas for improvement.
What role does leadership play in implementing a lean strategy?
Leadership plays a crucial role in implementing a lean strategy by setting a clear vision, providing necessary resources, and fostering a culture of continuous improvement. Leaders must actively support and participate in lean initiatives to drive organizational change.
Can a lean strategy be applied in service industries?
Yes, a lean strategy can be effectively applied in service industries. It focuses on improving service delivery processes, reducing wait times, enhancing customer interactions, and eliminating inefficiencies, ultimately leading to better service quality and customer satisfaction.
A strong corporate lean strategy primarily focuses on maximizing value while minimizing waste throughout an organization. This approach emphasizes the importance of understanding customer needs and aligning processes to deliver products and services that meet those needs efficiently. By adopting lean principles, companies can streamline operations, reduce costs, and enhance overall productivity, ultimately leading to improved customer satisfaction and competitive advantage.
Another critical aspect of a robust lean strategy is the continuous improvement mindset, often referred to as “Kaizen.” This involves fostering a culture where employees at all levels are encouraged to identify inefficiencies and propose solutions. By empowering teams to take ownership of their processes, organizations can drive innovation and adaptability, ensuring they remain responsive to market changes and customer demands.
Moreover, effective implementation of a lean strategy requires strong leadership and commitment from top management. Leaders must not only advocate for lean practices but also provide the necessary resources and training to support their teams. This commitment is essential for sustaining lean initiatives and achieving long-term success, as it establishes a foundation of accountability and continuous learning across the organization.
In summary, a strong corporate lean strategy is multifaceted, focusing on value creation, waste reduction, continuous improvement, and strong leadership. By integrating these elements, organizations can cultivate a lean culture that
Author Profile
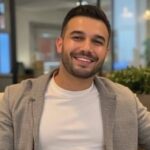
-
Alec Drayton is the Founder and CEO of Biracy, a business knowledge platform designed to help professionals navigate strategic, operational. And financial challenges across all stages of growth. With more than 15 years of experience in business development, market strategy, and organizational management, Alec brings a grounded, global perspective to the world of business information.
In 2025, Alec launched his personal writing journey as an extension of that belief. Through Biracy, he began sharing not just what he’d learned. But how he’d learned it through hands-on experience, success and failure, collaboration, and continuous learning. His aim was simple: to create a space where people could access reliable. Experience-driven insights on the many facets of business from strategy and growth to management, operations, investment thinking, and beyond.
Latest entries
- March 31, 2025Marketing & SalesDoes New Hampshire Impose Sales Tax on Car Purchases?
- March 31, 2025General Business QueriesHas the Professional Speaking Business Slowed Down: What Do the Trends Indicate?
- March 31, 2025General Business QueriesIs Dakota Arms Still In Business? Unraveling the Current Status of This Iconic Firearms Brand
- March 31, 2025Investment Queries And StrategiesIs Ocean Power Technologies a Smart Investment Choice in Today’s Market?