What Are Business Improvement Techniques and How Can They Transform Your Organization?
In today’s fast-paced and ever-evolving business landscape, organizations are constantly seeking ways to enhance their operations and maintain a competitive edge. Business improvement techniques serve as vital tools that empower companies to streamline processes, boost efficiency, and ultimately drive growth. Whether you’re a seasoned executive or a budding entrepreneur, understanding these techniques can unlock new avenues for success and innovation. This article delves into the essence of business improvement techniques, exploring their significance and the transformative impact they can have on an organization’s performance.
Business improvement techniques encompass a wide array of strategies and methodologies designed to identify inefficiencies and optimize workflows. From Lean and Six Sigma to Total Quality Management (TQM) and Agile practices, these approaches aim to foster a culture of continuous improvement within organizations. By systematically analyzing processes and implementing targeted changes, businesses can not only enhance productivity but also improve customer satisfaction and employee engagement.
Moreover, the implementation of business improvement techniques is not a one-size-fits-all solution; it requires a tailored approach that aligns with an organization’s unique goals and challenges. As we navigate through the various facets of these techniques, we will uncover how they can be effectively integrated into different business models, paving the way for sustainable growth and long-term success. Prepare to embark on a journey that will equip you with the
Understanding Business Improvement Techniques
Business improvement techniques encompass a variety of methodologies aimed at enhancing organizational performance, increasing efficiency, and maximizing profitability. These techniques are designed to identify areas of improvement within a business and implement systematic changes to achieve desired outcomes.
Common Business Improvement Techniques
Several widely recognized techniques can be employed to facilitate business improvement, each with its own focus and approach. Some of the most prevalent include:
- Lean Management: This technique emphasizes waste reduction without sacrificing productivity. It focuses on creating more value for customers with fewer resources.
- Six Sigma: A data-driven approach that seeks to improve quality by identifying and removing causes of defects and minimizing variability in manufacturing and business processes.
- Total Quality Management (TQM): A continuous improvement strategy that involves all members of an organization in improving processes, products, services, and the culture in which they work.
- Business Process Reengineering (BPR): This technique involves fundamentally rethinking and redesigning business processes to achieve dramatic improvements in critical measures of performance such as cost, quality, service, and speed.
- Kaizen: A Japanese term meaning “continuous improvement,” it focuses on incremental changes that enhance productivity over time.
Benefits of Implementing Business Improvement Techniques
Organizations that adopt business improvement techniques can experience numerous benefits, including:
- Enhanced operational efficiency
- Improved product quality and customer satisfaction
- Reduced operational costs
- Increased market competitiveness
- Greater employee engagement and morale
Comparison of Business Improvement Techniques
The following table provides a comparative analysis of several business improvement techniques based on key attributes:
Technique | Focus Area | Methodology | Key Benefits |
---|---|---|---|
Lean Management | Waste Reduction | Value Stream Mapping | Increased efficiency, reduced costs |
Six Sigma | Quality Improvement | DMAIC (Define, Measure, Analyze, Improve, Control) | Reduced defects, improved quality |
TQM | Quality Management | Continuous Improvement | Enhanced quality, customer satisfaction |
BPR | Process Redesign | Fundamental Rethinking | Major performance improvements |
Kaizen | Continuous Improvement | Incremental Changes | Enhanced productivity, employee involvement |
Challenges in Implementing Business Improvement Techniques
While the potential benefits of business improvement techniques are significant, organizations may face challenges during implementation. Common obstacles include:
- Resistance to change from employees
- Lack of management support or commitment
- Insufficient training and resources
- Inadequate data collection and analysis capabilities
By anticipating these challenges and addressing them proactively, organizations can better position themselves for successful implementation of business improvement techniques.
Understanding Business Improvement Techniques
Business improvement techniques encompass a variety of methodologies aimed at enhancing an organization’s processes, increasing efficiency, and delivering greater value to customers. These techniques can be applied across various industries to streamline operations, reduce waste, and improve overall performance.
Key Techniques in Business Improvement
- Lean Management
Lean management focuses on minimizing waste while maximizing productivity. Its principles include:
- Value: Define what is valuable from the customer’s perspective.
- Value Stream: Identify all the steps in the process and eliminate non-value-adding activities.
- Flow: Ensure that the process flows smoothly without interruptions.
- Pull: Produce only what is needed when it is needed.
- Perfection: Continuously seek ways to improve and eliminate waste.
- Six Sigma
Six Sigma is a data-driven approach aimed at reducing defects and improving quality. It uses statistical methods to identify and remove the causes of errors. The key elements include:
- Define: Clearly define the problem and project goals.
- Measure: Collect data and measure current performance.
- Analyze: Analyze data to identify root causes of defects.
- Improve: Implement solutions to improve processes.
- Control: Monitor the improved process to sustain gains.
- Total Quality Management (TQM)
TQM is an organization-wide approach focused on continuous improvement, customer satisfaction, and employee involvement. It emphasizes:
- Customer Focus: Prioritizing customer needs and satisfaction.
- Leadership: Strong leadership commitment to quality.
- Employee Involvement: Engaging all employees in the improvement process.
- Process Approach: Viewing processes as interconnected and aiming for efficiency.
- Kaizen
Kaizen, meaning “continuous improvement,” is a philosophy that encourages small, incremental changes in processes. Key principles include:
- Continuous Improvement: Regularly seek opportunities to improve.
- Employee Involvement: Encourage suggestions from all staff levels.
- Standardization: Establish standards to ensure consistency and quality.
Tools for Business Improvement
Tool | Description | Application |
---|---|---|
Value Stream Mapping | Visual representation of processes to identify waste | Lean Management |
Fishbone Diagram | Tool for identifying root causes of problems | Six Sigma |
PDCA Cycle | Plan-Do-Check-Act framework for continuous improvement | TQM and Kaizen |
5S | Workplace organization method (Sort, Set in order, Shine, Standardize, Sustain) | Lean Management |
Benefits of Business Improvement Techniques
Implementing business improvement techniques can lead to numerous benefits, such as:
- Increased efficiency and productivity
- Enhanced product or service quality
- Greater customer satisfaction and loyalty
- Reduced operational costs
- Improved employee morale and engagement
By adopting these techniques, organizations can create a culture of continuous improvement that not only meets current challenges but also prepares them for future growth and success.
Understanding Business Improvement Techniques Through Expert Insights
“Jessica Tran (Business Process Consultant, Efficiency Experts Inc.). Business improvement techniques are essential for organizations aiming to enhance productivity and reduce waste. By employing methodologies such as Lean and Six Sigma, businesses can systematically identify inefficiencies and implement sustainable solutions that drive long-term growth.”
“Mark Henderson (Operations Manager, Global Manufacturing Solutions). The key to successful business improvement techniques lies in fostering a culture of continuous improvement. Engaging employees at all levels in the process not only boosts morale but also leads to innovative ideas that can significantly enhance operational efficiency.”
“Linda Patel (Quality Assurance Director, Tech Innovations Corp.). Implementing business improvement techniques requires a data-driven approach. Utilizing analytics to measure performance and outcomes allows organizations to make informed decisions that align with their strategic objectives, ultimately leading to enhanced customer satisfaction and competitive advantage.”
Frequently Asked Questions (FAQs)
What is Business Improvement Techniques?
Business Improvement Techniques refer to methodologies and practices aimed at enhancing an organization’s processes, efficiency, and overall performance. These techniques include Lean, Six Sigma, Total Quality Management (TQM), and Continuous Improvement (CI), among others.
Why are Business Improvement Techniques important?
These techniques are essential for organizations to remain competitive, reduce waste, improve quality, and enhance customer satisfaction. They help identify inefficiencies and provide structured approaches to optimize operations.
What are some common Business Improvement Techniques?
Common techniques include Lean Management, which focuses on eliminating waste; Six Sigma, which aims to reduce defects; Kaizen, which emphasizes continuous improvement; and Business Process Reengineering (BPR), which involves redesigning processes for significant improvements.
How can organizations implement Business Improvement Techniques?
Organizations can implement these techniques by conducting thorough assessments of current processes, training employees on specific methodologies, setting measurable goals, and fostering a culture of continuous improvement throughout the organization.
What role does employee involvement play in Business Improvement Techniques?
Employee involvement is crucial as it encourages ownership of processes, fosters innovation, and ensures that improvements are practical and sustainable. Engaging employees at all levels enhances the effectiveness of improvement initiatives.
Can Business Improvement Techniques be applied to all types of businesses?
Yes, Business Improvement Techniques can be applied across various industries and sectors, including manufacturing, service, healthcare, and non-profit organizations. Adaptation of specific techniques may vary based on the unique needs and challenges of each business.
Business improvement techniques encompass a variety of methodologies and practices aimed at enhancing organizational performance, efficiency, and effectiveness. These techniques often include strategies such as Lean Management, Six Sigma, Total Quality Management, and Continuous Improvement processes. By employing these approaches, businesses can identify areas of waste, streamline operations, and ultimately deliver greater value to customers. The integration of these techniques fosters a culture of continuous improvement, empowering employees to contribute to the organization’s success.
Key takeaways from the discussion on business improvement techniques highlight the importance of data-driven decision-making and employee engagement. Organizations that leverage data analytics can gain insights into performance metrics, enabling them to make informed adjustments to their processes. Furthermore, involving employees in improvement initiatives not only boosts morale but also ensures that the solutions implemented are practical and effective, as those closest to the work often have valuable perspectives.
the successful implementation of business improvement techniques requires a commitment to fostering a culture of innovation and adaptability. Organizations that prioritize continuous improvement are better positioned to respond to market changes, enhance customer satisfaction, and achieve sustainable growth. By embracing these techniques, businesses can create a robust framework for ongoing development and operational excellence.
Author Profile
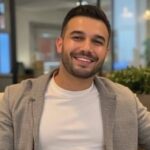
-
Aurelio Mills is the Founder and CEO of Biracy, a business knowledge platform designed to help professionals navigate strategic, operational. And financial challenges across all stages of growth. With more than 15 years of experience in business development, market strategy, and organizational management, Aurelio brings a grounded, global perspective to the world of business information.
In 2025, Aurelio launched his personal writing journey as an extension of that belief. Through Biracy, he began sharing not just what he’d learned. But how he’d learned it through hands-on experience, success and failure, collaboration, and continuous learning. His aim was simple: to create a space where people could access reliable. Experience-driven insights on the many facets of business from strategy and growth to management, operations, investment thinking, and beyond.
Latest entries
- March 31, 2025Marketing & SalesDoes New Hampshire Impose Sales Tax on Car Purchases?
- March 31, 2025General Business QueriesHas the Professional Speaking Business Slowed Down: What Do the Trends Indicate?
- March 31, 2025General Business QueriesIs Dakota Arms Still In Business? Unraveling the Current Status of This Iconic Firearms Brand
- March 31, 2025Investment Queries And StrategiesIs Ocean Power Technologies a Smart Investment Choice in Today’s Market?