Should You Track All Parts and Consumables in Your HVAC Business?
In the fast-paced world of HVAC (Heating, Ventilation, and Air Conditioning), maintaining efficiency and ensuring customer satisfaction are paramount. One often overlooked yet crucial aspect of running a successful HVAC business is the meticulous tracking of all parts and consumables. As technicians navigate through various projects, from installations to routine maintenance, the ability to monitor inventory levels, usage patterns, and costs can significantly impact profitability and operational effectiveness. But the question remains: do you track all parts and consumables in your HVAC business?
Effective inventory management goes beyond simply counting items on a shelf; it encompasses a comprehensive system that allows HVAC businesses to optimize their resources. By keeping a detailed record of parts and consumables, companies can reduce waste, prevent stockouts, and streamline their procurement processes. This not only saves time and money but also enhances service delivery, ensuring that technicians have the necessary tools and materials at their fingertips when they need them most.
Moreover, tracking parts and consumables can provide valuable insights into business trends and customer needs. By analyzing usage data, HVAC businesses can identify which products are in high demand, allowing for better forecasting and strategic planning. This proactive approach not only improves operational efficiency but also fosters stronger relationships with customers, as businesses can anticipate their needs and deliver tailored solutions. As we delve
Importance of Tracking Parts and Consumables
In the HVAC business, tracking all parts and consumables is crucial for several reasons. Accurate tracking helps manage inventory, reduces costs, and ensures timely service delivery. It allows businesses to maintain optimal stock levels, preventing both overstocking and stockouts, which can lead to inefficiencies.
Key benefits include:
- Cost Management: Keeping track of parts and consumables helps identify spending patterns and areas where costs can be reduced.
- Improved Efficiency: Knowing what parts are on hand allows for quicker response times to service calls, minimizing downtime.
- Customer Satisfaction: Timely access to necessary parts means faster repairs and installations, leading to happier customers.
- Inventory Accuracy: Regular tracking ensures that the inventory records reflect actual stock, reducing discrepancies and potential losses.
Methods for Tracking Parts and Consumables
There are several effective methods for tracking HVAC parts and consumables:
- Manual Tracking: This can be done using spreadsheets or physical logs. While low-cost, it is time-consuming and prone to human error.
- Inventory Management Software: Specialized software can automate tracking, providing real-time data on stock levels and usage rates.
- Barcode or RFID Systems: Implementing barcode scanning or RFID technology allows for quick updates and accurate tracking of inventory as it moves in and out.
- Regular Audits: Conducting periodic physical counts of inventory helps ensure that records match physical stock and identifies any discrepancies.
Key Components to Track
When tracking parts and consumables in your HVAC business, consider the following components:
Component | Description | Frequency of Tracking |
---|---|---|
Filters | Air filters, furnace filters, etc. | Monthly |
Refrigerants | Different types of refrigerants used | Weekly |
Coils | Evaporator and condenser coils | Monthly |
Motors | Compressor and blower motors | Quarterly |
Thermostats | Various thermostat models | Quarterly |
Tools | Specialized HVAC tools and equipment | Monthly |
By diligently tracking these components, HVAC businesses can maintain better control over their operations, improve service levels, and ensure they are always prepared to meet customer demands.
Incorporating a robust tracking system for parts and consumables is essential for the success of an HVAC business. By leveraging technology and implementing best practices, businesses can enhance efficiency, reduce costs, and provide superior service to their customers.
Importance of Tracking Parts and Consumables in HVAC
Tracking all parts and consumables in an HVAC business is crucial for several reasons. Accurate tracking helps maintain inventory levels, ensures timely service delivery, and optimizes operational efficiency.
- Inventory Management: Keeping precise records prevents overstocking or stockouts, which can disrupt service.
- Cost Control: Monitoring parts usage helps identify areas for cost reduction and waste elimination.
- Service Quality: Ensures technicians have the necessary tools and parts on hand, improving customer satisfaction.
Key Components to Track
To effectively manage your HVAC inventory, focus on the following components:
Component | Description |
---|---|
Parts | Major components like compressors, coils, and fans. |
Consumables | Items such as filters, refrigerant, and lubricants. |
Tools | Equipment used by technicians, like gauges and wrenches. |
Supplies | Miscellaneous items, including safety gear and cleaning supplies. |
Methods for Tracking Inventory
Several methods can be employed to track parts and consumables effectively:
- Manual Tracking: Using spreadsheets or physical logs. This method is simple but can be prone to errors.
- Inventory Management Software: Specialized software can automate tracking, making it easier to manage stock levels and orders.
- Barcode Scanning: Implementing barcodes on inventory items can streamline tracking and reduce human error.
Best Practices for Tracking
Adopting best practices can enhance your tracking efforts:
- Regular Audits: Conducting routine inventory checks helps maintain accurate records.
- Categorization: Organize parts and consumables into categories for easier access and tracking.
- Usage Reports: Analyze usage patterns to identify frequently used items and adjust inventory accordingly.
- Supplier Relationships: Maintain strong connections with suppliers for reliable restocking.
Challenges and Solutions
Tracking inventory can present challenges, but these can be mitigated with strategic approaches:
Challenge | Solution |
---|---|
Inaccurate Data | Regular audits and staff training on proper tracking methods. |
Stockouts | Implement reorder alerts in software or set minimum stock levels. |
Overstocking | Analyze sales data to adjust purchasing strategies. |
Time-Consuming | Automate processes using inventory management systems. |
Efficiently tracking all parts and consumables in your HVAC business is integral to operational success. By utilizing the right methods and adhering to best practices, you can ensure a streamlined inventory management process that enhances service delivery and profitability.
Expert Insights on Tracking Parts and Consumables in HVAC Businesses
Maria Sanchez (HVAC Business Consultant, Climate Solutions Group). “Tracking all parts and consumables in your HVAC business is essential for maintaining operational efficiency and ensuring customer satisfaction. A well-implemented inventory management system allows you to monitor stock levels, reduce waste, and avoid costly delays in service.”
James Thompson (Supply Chain Analyst, HVAC Innovations). “In the HVAC industry, accurate tracking of parts and consumables not only aids in inventory management but also enhances forecasting capabilities. By analyzing usage patterns, businesses can optimize their purchasing strategies and minimize overhead costs.”
Linda Chen (Operations Manager, EcoComfort HVAC Services). “Neglecting to track parts and consumables can lead to significant operational challenges. Implementing a comprehensive tracking system is crucial for ensuring that technicians have the necessary materials on hand, which directly impacts service quality and customer loyalty.”
Frequently Asked Questions (FAQs)
Do I need to track all parts and consumables in my HVAC business?
Yes, tracking all parts and consumables is essential for effective inventory management, cost control, and ensuring timely service delivery.
What are the benefits of tracking parts and consumables?
Tracking parts and consumables helps prevent stockouts, reduces excess inventory, improves order accuracy, and enhances overall operational efficiency.
How can I effectively track parts and consumables in my HVAC business?
Utilizing inventory management software can streamline tracking processes, automate reordering, and provide real-time visibility into stock levels.
What types of parts and consumables should I track?
You should track all major components such as compressors, coils, and thermostats, as well as consumables like filters, refrigerants, and lubricants.
How often should I review my inventory of parts and consumables?
Regular inventory reviews, ideally on a monthly basis, ensure that stock levels are optimized and help identify trends in usage and demand.
What challenges might I face when tracking parts and consumables?
Challenges include maintaining accurate records, managing supplier relationships, and adapting to fluctuating demand, which can complicate inventory management.
In the HVAC business, tracking all parts and consumables is essential for efficient operations and effective inventory management. By maintaining accurate records of parts and consumables, businesses can ensure that they have the necessary materials on hand to meet customer demands, reduce downtime during service calls, and minimize excess inventory costs. This practice not only enhances operational efficiency but also contributes to better financial management and forecasting.
Furthermore, implementing a robust tracking system allows HVAC businesses to monitor usage patterns and identify trends over time. This data can be invaluable for making informed purchasing decisions, optimizing stock levels, and planning for future growth. Additionally, having a clear understanding of inventory can help in managing supplier relationships and negotiating better terms based on usage data.
Ultimately, the effective tracking of all parts and consumables in the HVAC industry leads to improved customer satisfaction, as timely service and repairs are facilitated. By investing in inventory management systems and processes, HVAC businesses position themselves for long-term success and competitiveness in an ever-evolving market.
Author Profile
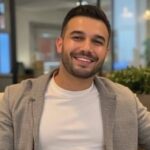
-
Aurelio Mills is the Founder and CEO of Biracy, a business knowledge platform designed to help professionals navigate strategic, operational. And financial challenges across all stages of growth. With more than 15 years of experience in business development, market strategy, and organizational management, Aurelio brings a grounded, global perspective to the world of business information.
In 2025, Aurelio launched his personal writing journey as an extension of that belief. Through Biracy, he began sharing not just what he’d learned. But how he’d learned it through hands-on experience, success and failure, collaboration, and continuous learning. His aim was simple: to create a space where people could access reliable. Experience-driven insights on the many facets of business from strategy and growth to management, operations, investment thinking, and beyond.
Latest entries
- March 31, 2025Marketing & SalesDoes New Hampshire Impose Sales Tax on Car Purchases?
- March 31, 2025General Business QueriesHas the Professional Speaking Business Slowed Down: What Do the Trends Indicate?
- March 31, 2025General Business QueriesIs Dakota Arms Still In Business? Unraveling the Current Status of This Iconic Firearms Brand
- March 31, 2025Investment Queries And StrategiesIs Ocean Power Technologies a Smart Investment Choice in Today’s Market?